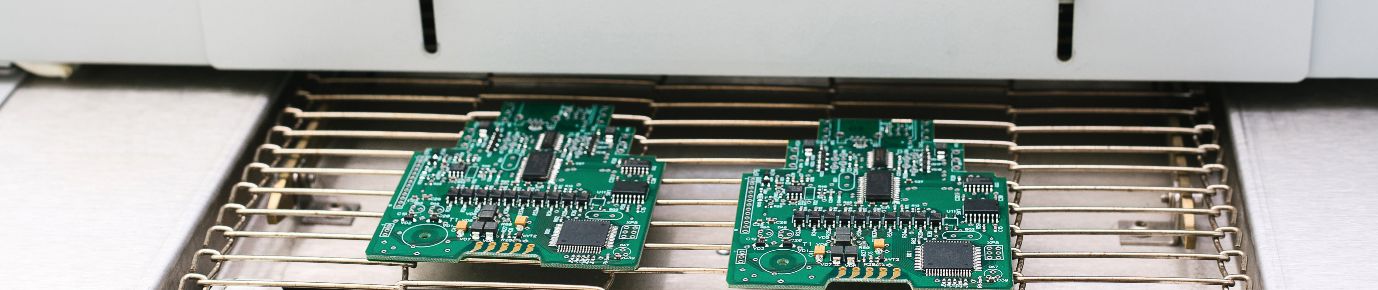
Vacuum Furnace Brazing 101
In industries where every micron counts, from the intricate circuits of electronics to the high-stakes world of aerospace, vacuum furnace brazing is a testament to how precision can convert a simple process into a critical technology. Vacuum furnace brazing, a method of joining metal components in a high-vacuum environment, offers enhanced joint integrity, uniformity of finished products and reduced thermal distortion due to the absence of atmospheric gasses. This process is particularly beneficial for creating complex and delicate assemblies, where precision and strength are essential.
Benefits Over Traditional Brazing Methods
The innovative vacuum furnace brazing process offers several compelling benefits over traditional brazing methods, making it a superior choice for various industrial applications. Here's an expanded look at these advantages:
Exceptional Quality and Uniformity
- In vacuum furnace brazing, the absence of air and the controlled environment prevent oxidation and contamination, leading to cleaner and stronger joints.
- Uniform heat distribution ensures consistent brazing quality across the entire piece, which is crucial for complex assemblies and high-precision components.
Enhanced Strength and Durability
- Joints created by a brazing vacuum furnace are notably stronger due to the even distribution of brazing filler, reducing weak spots.
- This method enhances the product's lifespan, offering better resistance to thermal and mechanical stresses.
Cost-Effective and Efficient
- The vacuum furnace brazing process reduces material waste and energy consumption, which leads to significant cost savings.
- Minimizes the need for post-brazing treatments, further reducing production time and costs.
Eco-Friendly Approach
- Generates fewer emissions and requires less energy, aligning with sustainable manufacturing practices.
- Helps industries meet environmental regulations and reduce their carbon footprint.
Versatility in Applications
- Suitable for various metals and alloys, vacuum brazing applications extend across many sectors, including aerospace, automotive and medical devices.
- Allows for joining dissimilar materials, offering greater design flexibility and innovation in product development.
Precision and Control
- The ability to precisely control temperature and environment in vacuum brazing allows for intricate and delicate metal joining, which is essential in high-precision industries.
- Ensures minimal distortion and shrinkage, crucial for maintaining dimensional accuracy in complex components.
Industries Utilizing a Braze Oven
The braze oven is indispensable in a broad spectrum of industries. Its popularity isn't surprising, given the process's high reproducibility and the strong, reliable bonds it creates between metals. Here's an overview of the key industries that extensively utilize vacuum brazing applications:
- Aerospace: In an industry where every component must withstand extreme conditions, vacuum furnace brazing is crucial for creating solid and reliable joints in aerospace parts.
- Heavy Machinery: A brazing oven is instrumental in manufacturing large machinery parts, ensuring durability and resistance to mechanical stress.
- Medical Components: Precision is paramount in the medical field, and vacuum brazing furnaces facilitate the creation of intricate, high-strength joints in medical devices.
- Electronics: The technology is vital for producing small, precise joints in electronic components, where consistency and reliability are essential.
- Nuclear Engineering: Given the critical nature of nuclear components, the consistent quality and strength provided by a brazing vacuum furnace are indispensable.
- Petrochemicals: In an industry dealing with corrosive substances and high temperatures, the robust joints created by vacuum furnace brazing are a necessity.
- Transportation: The vacuum furnace brazing process plays a critical role in manufacturing durable, reliable components for modes of transportation ranging from automobiles to railways.
- Shipbuilding: The structural integrity of ships heavily relies on the strong bonds formed by vacuum brazing, ensuring safety and durability in marine environments.
Rely on Sentro Tech for High-Quality Brazing Ovens
Sentro Tech is a distinguished choice for brazing solutions thanks to custom-built vacuum brazing ovens tailored to meet specific client requirements. Our furnaces offer unmatched joint integrity and uniformity essential for diverse industries. Combining customization, cutting-edge technology and dedicated customer support makes Sentro Tech the ideal partner for all your brazing needs. Let's talk about building your braze oven today!
Contact a SpecialistBrazing Oven: Frequently Asked Questions
As with any advanced technology, there are always questions about how they work and what makes them unique. Here, we address some of the most common queries to provide a clearer understanding of the brazing oven and the advantages of furnace brazing:
How Does Vacuum Brazing Work?
Vacuum brazing is a process in which metal parts are joined with the help of a filler metal with a melting point that's lower than the base metals. In a vacuum environment, the absence of air and other gasses ensures a clean, oxide-free joint, which enhances the strength and integrity of the bond.
What Metal Cannot Be Brazed?
Generally, cast iron is a metal that is challenging to braze due to its high carbon content, which can lead to brittleness in the joint. Additionally, some high-carbon steels and metals with special coatings or oxides can also be difficult or impractical to braze. It's important to note that while difficult, brazing cast iron and certain other metals is not impossible but requires special techniques, brazing alloys and fluxes.
What Are the 4 Heating Techniques Used for Brazing?
The four primary heating techniques used in brazing include Torch Brazing, where a gas flame torch heats the metal parts for small-scale or detailed work; Furnace Brazing, which uses a furnace for uniform heating suitable for mass production in vacuum or controlled atmospheres; Induction Brazing, employing electromagnetic induction for precise, quick heating ideal for high-volume jobs; and Dip Brazing, involving immersing parts in a molten brazing alloy bath, ensuring even heating for parts needing substantial filler material.
High Temperature Vacuum Furnaces
Designed to serve a diverse array of heat treatment processes, each Sentro Tech vacuum furnace is customizable in size, ensuring a perfect fit for your specific needs and budget constraints.