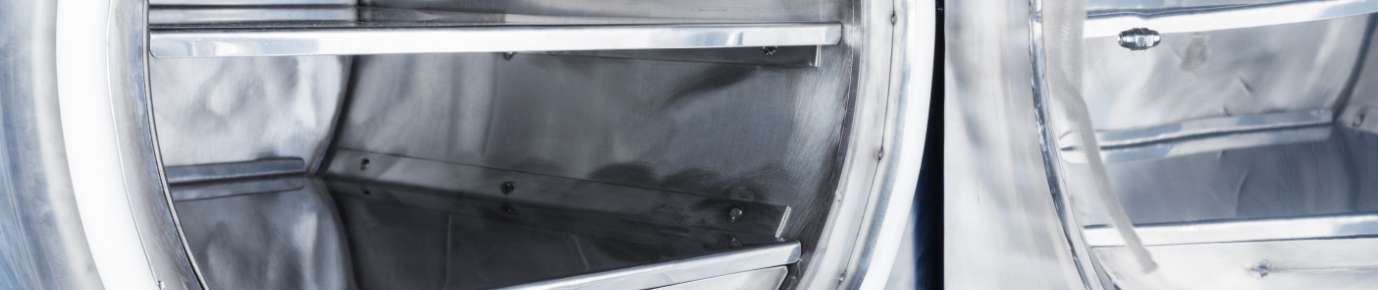
What Is a Vacuum Furnace?
Sometimes referred to as a controlled atmosphere furnace, a vacuum furnace is any furnace that removes air from the heating chamber during operation. A vacuum furnace system does this by utilizing an air purging pump and creating a seal that does not allow oxygen to enter the chamber while it is in use.
Temperature is controlled by various means but is uniform across the heating chamber. Most vacuum furnace systems have a maximum operating temperature between 1,500 and 5,400 degrees Fahrenheit.
Removing oxygen from the heating process eliminates the possibility for metal parts to oxidize under rapid temperature increase. Oxidation causes metals to lose electrons and break down, making their bonds weaker.
With oxidation removed as a possibility inside a vacuum furnace, heat treatment of metals and ceramics through annealing, brazing, sintering and other techniques results in a higher purity end product free of contaminants and defects caused by atmospheric gases.
Parts of a Vacuum Furnace
The number of parts needed to operate a vacuum furnace is basically the same as a standard industrial furnace or oven. The big change is the pumping system that pulls the air out of the airtight chamber during the heating process. All told, the list of vacuum furnace components includes the vacuum system and:
- Airtight Furnace Chamber
- Electric Heating Element
- Temperature Controls
- Furnace Shell
- Transport Apparatus
- Power Supply System
The Vacuum Furnace Process
Vacuum furnace processing requires several different components working in tandem to create an atmosphere that prevents oxidation and heat loss from the product. Before we go into a little more detail, here are the steps to the vacuum furnace process:
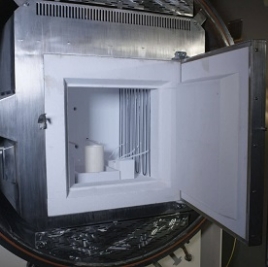
1. Load the Furnace
The vacuum furnace heat treatment process begins by placing the parts, tools or components into the chamber. Depending on furnace size, this can be accomplished using a rolling rack or tray to load parts. For smaller vacuum furnaces, simply open the chamber and place parts inside.
2. Create a Vacuum Inside the Chamber
After closing and sealing the chamber, the next step in vacuum furnace processing is to create a vacuum inside the chamber. Initialize the pump to remove all of the oxygen inside the vacuum furnace and maintain an airtight seal.
3. Heat Your Parts
Use the temperature controls to heat your parts. Most vacuum furnace systems have fine controls that manage the temperature to a precise degree. The speed at which the vacuum furnace reaches the desired temperature can also be managed.
4. Cooling and Finishing
The manner in which you cool parts following a vacuum furnace heat treatment will differ depending on the material and the application. One of the more common ways to cool components in vacuum furnace processing is to cycle inert gases such as argon into the heating chamber. Because inert gases do not readily undergo chemical reactions, they are an ideal choice as a cooling system for your vacuum furnace.
Other vacuum furnace processes such as quenching can rapidly cool products and drastically reduce production cycles.
Contact SentroTech For Vacuum Furnace Systems
SentroTech designs and manufactures vacuum furnace systems, industrial ovens and other furnaces for dozens of industries and applications. Our custom high-temperature atmospheric vacuum furnaces can be built with dozens of options and configurations including data recording, mass flow controllers and pressure gauges. To learn more about how a vacuum furnace works or to purchase one for your enterprise, contact the industrial furnace professionals at SentroTech today.
Contact Us