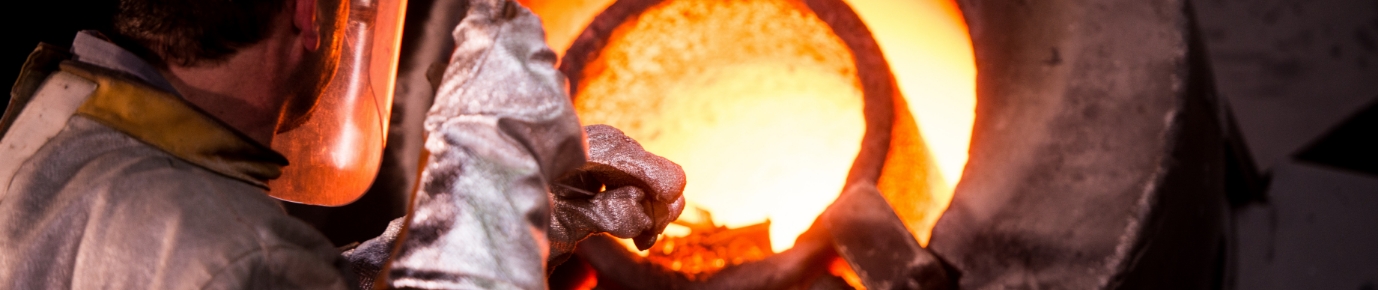
What Role Does a Foundry Furnace Play in Metalworking?
A foundry furnace's main function is to melt metal materials so that they can be poured into molds to create various products. Foundry furnaces are used to melt a wide range of metals, including iron, steel, aluminum, brass, bronze, and more. Foundry furnaces ovens are used for a variety of applications across many industries including architecture, railroads, farming and more.
Once the metal is melted in the furnace, it is typically poured into molds or castings to create a variety of products, such as engine blocks, pipes, tools, and decorative items. The molds are designed to create the desired shape of the final product and are often made of sand, plaster, or other materials that can withstand the high temperatures of the molten metal.
Overall, the foundry furnace is a critical component of any metalworking operation. It allows foundries to melt and shape metals into a variety of products, from small decorative items to large industrial parts, and plays an essential role in the manufacturing industry.
1. Cupola Furnaces
A cupola furnace is a type of foundry furnace used for melting and casting iron. It is named after its shape, which resembles a cup or a dome. The cupola furnace is made of a cylindrical shell (typically made of steel plate), lined with refractory bricks, and other heat-resistant materials. A cupola furnace is typically 30 to 80 feet tall, and its diameter can range from 5 to 13 feet.
The cupola furnace is loaded with a combination of iron ore, coke (carbon), and limestone, which are added in layers. A blast of hot air is then blown into the furnace through nozzles at the bottom heating the materials and causing them to melt and react chemically. The coke burns, producing carbon monoxide, which reacts with the iron oxide in the ore, reducing it to molten iron. The limestone helps to remove impurities by forming slag, which floats on top of the molten iron and can be skimmed off.
Once the molten iron has accumulated in the bottom of the furnace, it is tapped through a hole and collected in ladles for pouring into molds. The cupola furnace is a highly efficient and reliable foundry furnace for producing cast iron, and it has been used for centuries in the industry. However, it is also a significant source of air pollution, as the combustion of coke produces large amounts of carbon dioxide and other pollutants.
2. Electric Arc Furnaces
An electric arc furnace (EAF) is a type of foundry furnace that is used to melt and refine metals, particularly scrap steel. The electric arc furnace uses electric arcs created by large graphite electrodes to melt the metal. The furnace is typically made of a large steel shell lined with refractory material, and the electrodes are lowered into the furnace to create an electric arc between them and the metal.
The intense heat generated by the arcs melts the scrap, which then undergoes refining by the addition of various materials, such as lime or fluorspar, to remove impurities. Once the desired level of purity is achieved, the molten metal is tapped from the foundry furnace and poured into molds for further processing.
One of the advantages of the electric arc furnace is that it can be used to recycle scrap steel, reducing the need for new raw materials and decreasing the amount of waste generated. Additionally, because the EAF uses electricity as a fuel source, it can be more environmentally friendly than other types of furnaces that rely on fossil fuels.
3. Induction Furnaces
Another type of foundry furnace is the induction furnace, which is used to melt various metals. It utilizes electromagnetic induction to heat and melt metal by creating electrical currents within the metal itself. The induction furnace consists of a coil of copper tubing that is heated by alternating current, which creates a magnetic field. This magnetic field causes eddy currents in the metal, which generates heat and melts the metal.
The induction furnace can be used to melt a variety of metals, including iron, steel, copper, and aluminum. It is commonly used in foundries and metalworking shops for melting and casting metals into various shapes and forms.
Induction furnaces come in a range of sizes, from small, handheld units to large, industrial-scale foundry furnaces used in steel mills and other heavy industries. They offer several advantages over other types of foundry furnaces, including faster heating times, higher energy efficiency, and better temperature control. They also produce fewer emissions and generate less waste, making them a more environmentally friendly option.
4. Crucible Furnaces
A crucible furnace is a type of foundry furnace used for melting and casting metals that have a low melting point such as brass, bronze, and aluminum. It is called a "crucible" furnace because the metal is melted in a crucible, a container made of a heat-resistant material such as graphite, clay, or ceramic.
The crucible furnace typically consists of a furnace chamber made of refractory material, which is heated by a fuel source such as natural gas, propane, or electricity. The crucible is placed inside the furnace chamber and heated until the metal inside it melts.
Once the metal has melted, it can be poured into molds to create various shapes and forms. The crucible can be removed from the furnace chamber using tongs or other tools, and the molten metal can be poured into the molds.
Crucible furnaces come in a variety of sizes, from small, tabletop units used in jewelry making and small-scale metalworking to larger, industrial-scale furnaces used in larger foundries and manufacturing facilities. They are relatively easy to use and maintain and are a cost-effective way to melt and cast small to medium-sized quantities of metal.
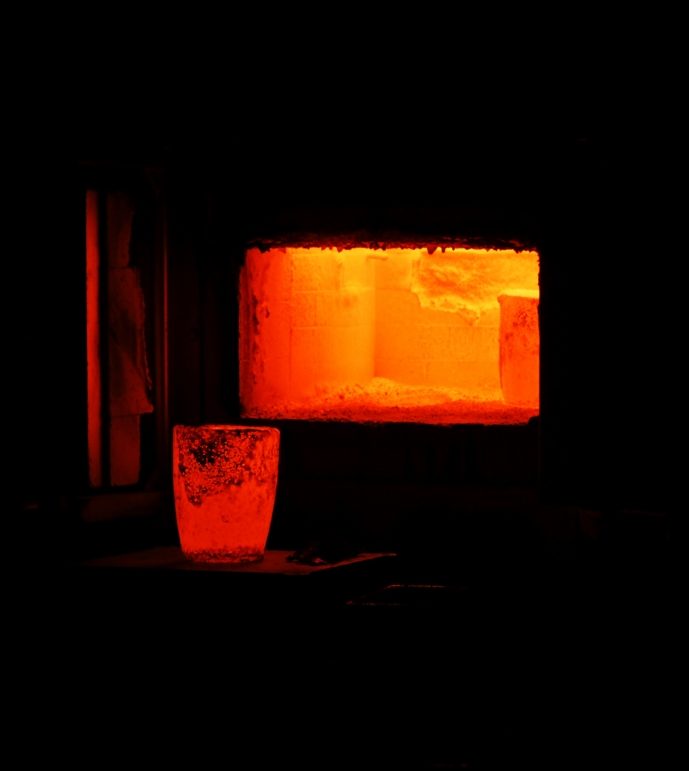
5. Blast Furnaces
The last type of foundry furnace we'll go over is the blast furnace, which is used in the production of iron and steel. It is a large, vertical furnace that is used to melt iron ore and other materials, such as limestone and coke, to create pig iron, which is used as a raw material in the production of steel.
The blast furnace operates by heating a charge of iron ore, limestone, and coke in the presence of hot air that is blown into the furnace through a series of nozzles. The hot air reacts with the coke, producing carbon monoxide, which reduces the iron ore to its elemental form. The limestone is added to the furnace to remove impurities and form a slag, which is skimmed off the surface of the molten iron.
The blast furnace is typically made of a steel shell lined with refractory material and is operated continuously for several years. The furnace is charged with raw materials at the top and molten iron is tapped off from the bottom periodically.
One of the main advantages of the blast furnace is its ability to produce large quantities of iron and steel at a relatively low cost. The blast furnace has been used for centuries and is still widely used today in the production of steel. However, it is also a major source of greenhouse gas emissions, as the process of heating the furnace requires large amounts of fossil fuels.
Contact Sentro Tech for a Custom Foundry Furnace
Sentro Tech is a leading designer and builder of custom foundry furnaces in the United States. With decades of experience manufacturing high-quality furnaces for a range of applications, we have the expertise and knowledge to create a custom solution tailored to your specific needs. Our team of experts will work with you during every step of development, from the design phase all the way through to delivery and installation. Sentro Tech can develop a comprehensive package for all types of foundry furnaces. Contact us to get started on your next foundry furnace project today!
Contact Us