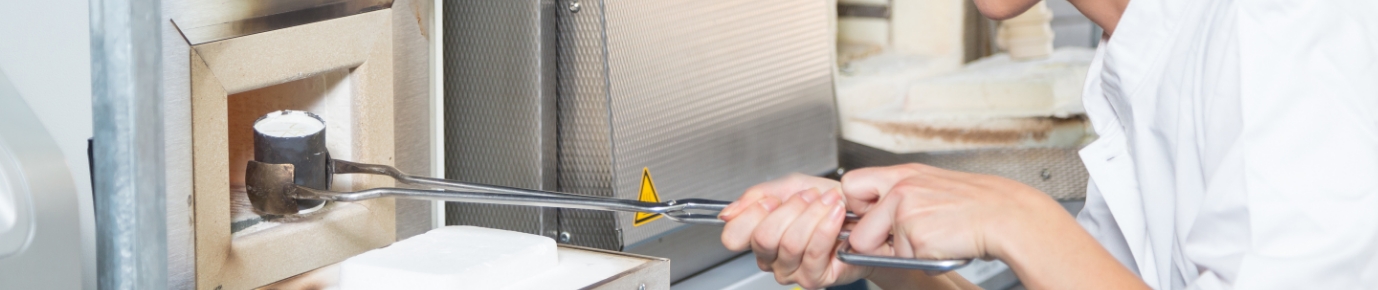
What Is Tempering?
The first order of business is addressing the question, "What is tempering?" The tempering process is a heat treatment technique used primarily to enhance the toughness of iron-based alloys, making them less prone to brittleness. Tempering involves heating the metal to a certain temperature below its critical point and then allowing it to cool under controlled conditions. This method is instrumental in adjusting the physical properties of the metal, including its hardness and strength. The success of the tempering process relies heavily on precision in temperature control and timing, ensuring that the metal achieves the desired characteristics without compromising its structural integrity.
Understanding Tempering Ovens
Tempering ovens are specialized equipment designed to fine-tune the properties of metals through controlled heating and cooling processes. These ovens are crucial in the tempering process, where their ability to maintain precise temperatures is prime directive. By carefully adjusting the temperature within the oven, technicians can alter the metal's internal structure, enhancing its toughness and reducing susceptibility to cracks and breaks. This ensures that metals achieve the perfect balance of hardness and elasticity, essential for applications demanding durability and strength. The significance of tempering ovens extends beyond their functionality; they represent a blend of science and art in the quest to achieve the desired characteristics in metals, making them indispensable in the metalworking industry.
Step-by-Step Guide to Using Tempering Ovens
Navigating the tempering process with tempering ovens is a fascinating journey from preparation to completion. Here's a straightforward guide to ensure you get the most out of your tempering efforts:
- Preparation: Begin by thoroughly cleaning the metal pieces to remove any surface impurities or residues. This prevents any inconsistencies during the tempering process. Properly preparing the metal ensures that the heat treatment is uniformly applied, leading to more predictable and desirable characteristics in the final product.
- Preheating: Before introducing the metal, preheat your tempering oven to the specific temperature required for your metal type. This temperature varies significantly depending on the alloy and the desired physical properties. Preheating the oven ensures that the metal is exposed to a consistent temperature as soon as it's placed inside, which is critical for achieving the desired outcome.
- Placement: Carefully place the prepared metal inside the oven, ensuring it's positioned to allow for optimal air circulation around it. This provides even heating and avoids hotspots, which could lead to uneven tempering. The arrangement of the metal pieces inside the oven can significantly affect the tempering process's efficiency and effectiveness.
- Tempering: Heat the metal for the predetermined time required to achieve the desired hardness and toughness. Depending on the metal's thickness and composition, this period can range from a few minutes to several hours. Consistency in timing is crucial as it directly influences the metal's final properties.
- Monitoring: Throughout the tempering process, closely monitor the oven's temperature to ensure it remains steady. Fluctuations in temperature can alter the metal's structural integrity, potentially leading to suboptimal characteristics. This constant vigilance helps maintain the precision necessary for a successful tempering process.
- Cooling: After the tempering time has elapsed, allow the metal to cool down. This can be done either inside the oven with the power off, promoting a gradual cooling process or by removing the metal to air cool in a controlled environment. The cooling method plays a significant role in determining the metal's final structure and properties.
Types of Metals Suitable for Tempering
The tempering process significantly enhances the performance and durability of various metals, making it a key technique in many industries. Here's a closer look at the types of metals that benefit most from tempering:
- Carbon Steel: Widely used for its affordability and strength, carbon steel becomes even more durable and resistant to wear after tempering.
- Alloy Steel: This metal's versatility is enhanced by tempering, which improves its ability to withstand stress without becoming brittle.
- Stainless Steel: While it's known for its corrosion resistance, tempering stainless steel further increases its toughness, making it suitable for various applications.
- Tool Steel: Tools made from this metal are hardened and then tempered to achieve a balance of hardness and toughness, essential for cutting and machining tasks.
- Spring Steel: Tempering is crucial for spring steel, as it enhances its elasticity and ability to return to the original shape after bending or twisting.
Each of these metals undergoes tempering to achieve specific properties tailored to their applications, from automotive components to construction materials and beyond. The tempering metal process extends the life of these materials and enhances their performance in demanding environments.
Frequently Asked Questions: Tempering Process
The tempering process often raises questions among those new to metalworking or considering tempering for their projects. Below, we address some of the most common inquiries.
What Is the Difference Between Annealing and Tempering?
While both processes involve heat treatment, annealing softens the metal, improves its ductility and relieves internal stresses. In contrast, tempering aims to increase toughness and reduce brittleness without significantly reducing the metal's hardness.
What Is the Best Temperature for Tempering Steel?
The ideal tempering temperature for steel varies depending on the desired balance of hardness and toughness. Generally, tempering is performed at temperatures between 125°C (255°F) and 700°C (1292°F), with specific temperatures selected based on the steel's composition and the application's requirements.
What Are the Signs That a Metal Needs Tempering?
Metals that are too hard, brittle or have uneven physical properties may require tempering. This process can restore or enhance the metal's performance characteristics, making it more suitable for its intended application.
Can All Metals Be Tempered?
Not all metals benefit from tempering. The process is most effective on iron-based alloys such as steel. Metals without iron content, like copper and aluminum, undergo different heat treatment processes to achieve similar improvements in toughness and durability.
How Long Does the Tempering Process Take?
The duration of the tempering process can vary from a few minutes to several hours, depending on the type of metal and the desired outcome. The key is to allow enough time for the heat to evenly penetrate and alter the metal's internal structure.
Get Fired Up With Sentro Tech's Tempering Ovens
Sentro Tech's high-quality tempering ovens provide the precise temperature control and uniformity essential for the tempering process, ensuring that each piece of metal achieves the ideal balance of toughness and durability. Our expertise and dedication to innovation make Sentro Tech your best choice for enhancing the performance and longevity of your metal components. Explore our industrial furnaces, ovens and furnace heating elements and request your quote today!
High-Temperature Furnaces, Kilns, Ovens & More
Sentro Tech Corporation provides an extensive array of high-temperature processing solutions, from compact laboratory furnaces and box furnaces to tube furnaces, as well as large-scale ceramic kilns and vacuum furnaces suitable for production settings.