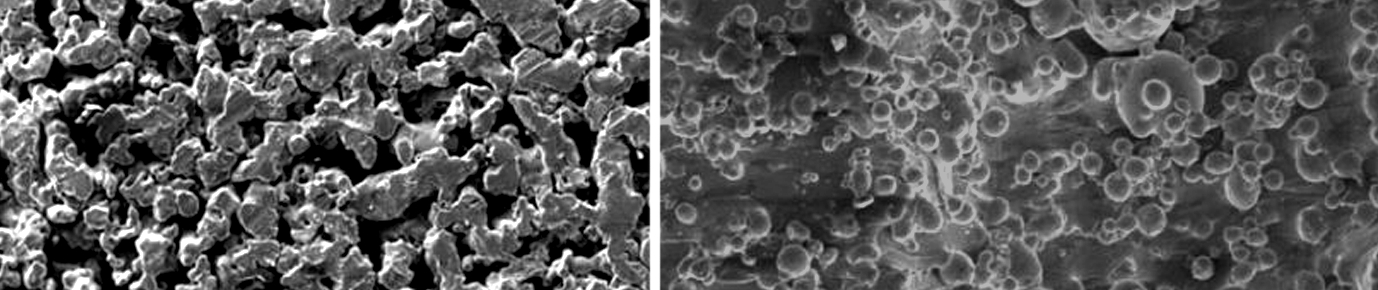
What Is Sintering?
At its most basic level, sintering applies pressure and heat to fuse metal powders. On a molecular level, powder sintering diffuses the atoms in the metal across the boundaries of the particles, creating one solid piece. Powder metallurgy differs from soldering, which doesn't require pressure and melts an alloy to join two metal parts together. Sintering can be used in additive manufacturing with 3D metal printers. The sintering temperature is always below the material's melting temperature. A simple example of sintering is the creation of a snowball by compressing loose snow in your hands.
What Is Sintered Metal?
Metal powder sintering is often used to form refractory metals like tungsten or molybdenum, which generally don't melt because of their high melting temperatures. Occasionally, a brazing alloy that melts is applied during heat treatment to partially infiltrate each part and create a stronger joint. Sintering's key function is to fuse metal, but it also offers other benefits, like:
- Reduced porosity
- Enhanced strength
- Improved electrical conductivity
- Increased translucency
- Better thermal conductivity
Sintering Furnaces from Sentro Tech
Sentro Tech is a leader in customizing and manufacturing high-temperature furnaces to meet our customers' specifications. We understand your needs and can develop sintering furnaces to meet your exact requirements. Contact us to learn more.
Contact UsWhat Is Melting?
In the sintering vs. melting discussion, the definition of melting is straightforward: applying enough heat to transform material from a solid state to a liquid. On a molecular level, as the temperature increases, the ions in the metal vibrate more and more, eventually breaking their bonds and moving freely. Once the bonds are loosened, and the material's internal structure shifts, it becomes a liquid. Different melting temperatures are often required when combining two or more metals since each material has its own melting point. Some metals, like iron and nickel, melt relatively easily, while refractory metals, as mentioned before, don't melt under normal conditions.
The Uses Of Melting
Melting is sometimes used to change a metal's physical characteristics, but its most frequent use is to prepare metal for casting. In casting, the manufacturer pours molten metal into a die or mold to create a part. Patterns for casting can be made of molding sand, wax or other metals. Casting is particularly useful in manufacturing intricate or large components, such as an engine block. Disadvantages of casting include:
- A time-intensive cooling process
- Difficulty in keeping tight dimensional tolerances
- The need for additional machining
The Process of Sintering Metal
Sintering metal or steel involves several steps. The first phase heats the metals to a temperature that will create martensitic, crystalline structures. Then the materials are compacted. Cold welds sometimes provide additional strength for the compacted powders. In the next phase, elements such as copper powder or cemented carbides are added to the compacted materials. This stage will involve either the transient or permanent liquid phase sintering process depending on the metals used. In the last phase, a liquid and binder additive is introduced to flow into any remaining pores in the metal. Another way to view the sintering process is through these stages:
- Removing lubricants
- Reducing oxides
- Bonding particles
- Cooling
The variables that affect sintering include atmosphere, temperature and cooling rate. Sintering can occur in atmospheres like air, vacuum and argon/nitrogen. High-temperature sintering offers several advantages, including increases in:
- Tensile strength
- Bending fatigue strength
- Impact energy
Trust Sentro Tech with Your Sintering Furnace Needs
Sentro Tech designs and manufactures sintering furnaces that can operate in partial vacuum and positive vessel pressure. Our standard furnaces operate at temperatures up to 1400°C to 1700°C, but we can customize your industrial furnace to meet your exact specifications. Contact us today to learn how a sintering furnace from Sentro Tech can improve your application.
Contact Us