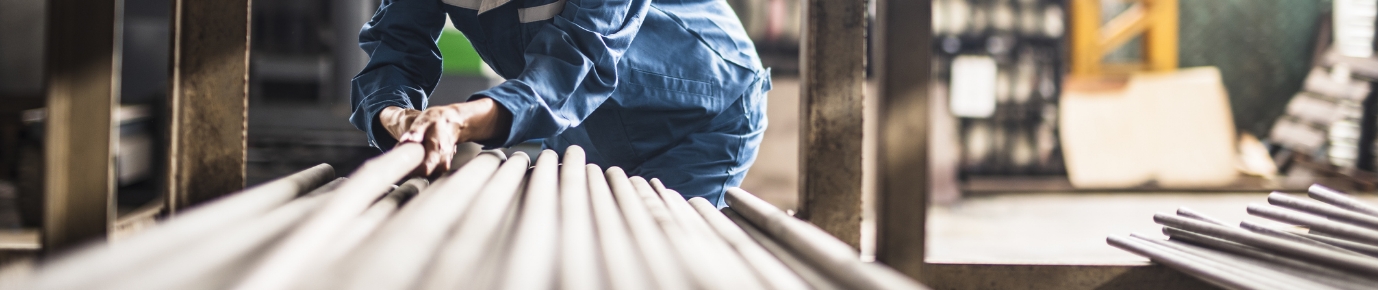
The Role of Basic Oxygen Steelmaking
Basic oxygen steelmaking represents a revolutionary advancement in the industry, marking a departure from less efficient, more time-consuming traditional methods. At the heart of this innovation is the utilization of high-purity oxygen, which significantly accelerates the conversion of raw iron into steel.
This process boasts rapid processing times and emphasizes energy efficiency and the capability to handle large volumes of material. Such advancements have streamlined the production process while improving the quality of the steel produced, making basic oxygen furnaces a cornerstone in modern steelmaking.
The Basic Oxygen Process (BOP)
The basic oxygen process transforms steelmaking with its efficiency and technological sophistication. By injecting high-purity oxygen into molten iron, impurities are effectively removed, leading to the production of high-quality steel. This method excels in efficiency and adapts easily to large-scale production needs. Let's break down the steps involved in more detail:
- Introduction of Molten Iron: The process begins by introducing hot molten iron into the basic oxygen furnace. This step is crucial as it prepares the foundation for the oxygen-based refinement that follows, setting the stage for the transformation of iron into steel
- Oxygen Injection: At this stage, high-purity oxygen is blown into the furnace at speeds exceeding the speed of sound, rapidly reacting with carbon to reduce its content in the melt. This reduction is vital for controlling the steel's final properties and quality.
- Temperature and Chemical Adjustments: To fine-tune the steel's characteristics, fluxes such as lime or dolomite are added, adjusting the steel's chemical composition and temperature. These adjustments are necessary to achieve the desired quality and ensure the steel meets specific industry standards.
- Tapping the Steel: The tapping process is the culmination of basic oxygen steelmaking, where the refined steel is transferred from basic oxygen furnaces into ladles. This step is critical for the subsequent casting or further processing, marking the transition from raw production to the creation of usable steel products.
Key Advantages of the Basic Oxygen Process
The basic oxygen process combines efficiency with environmental sustainability. Below are the advantages that set basic oxygen furnaces apart from traditional steelmaking equipment.
Energy Efficiency
The basic oxygen steelmaking process stands out for its remarkable energy efficiency. It significantly reduces the energy required to produce steel, lowering production costs and contributing to a smaller environmental footprint, aligning with global efforts toward sustainable manufacturing.
Rapid Processing
Speed is of the essence in steel production, and basic oxygen steelmaking excels in this area. The process can convert molten iron into steel in minutes, greatly enhancing productivity and meeting the demands of large-scale production.
High Volume Capacity
Because it's designed to handle large batches, a BOF furnace is ideal for operations that require the production of substantial quantities of steel. This capability ensures supply can keep pace with demand, a crucial factor for industries reliant on steel.
Environmental Benefits
Basic oxygen steelmaking significantly reduces greenhouse gas emissions compared to older methods. By emitting fewer pollutants, the basic oxygen process supports the steel industry's move toward more environmentally friendly practices.
Why Choose Sentro Tech for Your Oxygen Furnace Needs
Choosing Sentro Tech for your basic oxygen furnace means partnering with a leader in high-temperature furnace technology. Here's why Sentro Tech stands out:
- Expertise and Innovation: Sentro Tech has 25+ years of experience designing and manufacturing oxygen furnaces that meet the rigorous demands of modern steelmaking. Our commitment to innovation ensures that Sentro Tech clients receive the most advanced solutions available.
- Custom Solutions: We understand that each steel production facility has unique needs, which is why we specialize in custom industrial furnace designs. Whether you're upgrading your existing facility or building a new plant, we offer solutions that fit your specific requirements.
- Responsive Professional Service: The Sentro Tech team is dedicated to providing the best oxygen furnace technology along with outstanding customer service. From the initial consultation to after-sales support, we're here to ensure your operations run smoothly and efficiently.
Sentro Tech | High-Temperature Furnace Manufacturer
Sentro Tech Corporation provides a range of high-temperature box and tube furnaces suited for various applications. Whether you need a compact laboratory furnace, a large-scale production kiln or a custom-designed furnace made to your specs, we have the solution.
FAQs About Basic Oxygen Furnaces
Let's address common questions surrounding basic oxygen furnaces (BOF) to help demystify the process and its importance in steel production. Please contact us if you'd like additional information.
What Are the Limitations of BOF?
While BOFs are highly efficient for large-scale steel production, they require a significant upfront investment in infrastructure and operation. Additionally, the process is primarily suited for producing large quantities of steel, which may not be as workable for smaller, bespoke orders.
What Is the Difference Between BOF and EAF Steelmaking?
The difference lies in their heat sources: BOFs use high-purity oxygen to reduce iron's carbon content, while EAFs (Electric Arc Furnaces) melt scrap steel using electric arcs. BOFs are typically used for large-scale production from iron ore, whereas EAFs are used primarily to melt small or large batches of scrap metal.
Why Is Oxygen Used in Steel Production?
Oxygen plays a critical role in removing impurities such as carbon, silicon, phosphorus and manganese from molten iron. By blowing high-purity oxygen into the furnace, these elements react to form gases or slag, which can be easily removed, resulting in purer BOF steel.
Boost Production With Basic Oxygen Furnaces From Sentro Tech
Sentro Tech's advanced basic oxygen furnaces can improve your steel production. Our technology is designed to boost efficiency, quality and sustainability in your operations. With our expert support and innovative solutions tailored to your needs, you'll experience unmatched performance and cost savings. Looking for a different type of furnace? Check out our entire selection of high-temperature ovens and furnaces today!